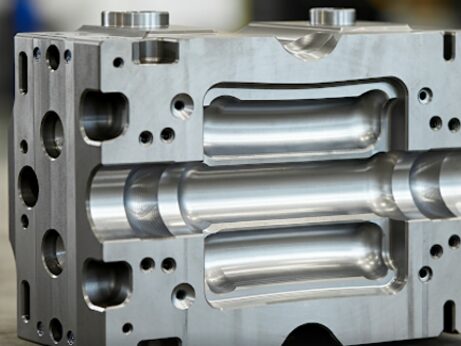
製缶板金加工は、金属板を切断、曲げ、溶接などの工程を経て、箱型や筐体など、三次元形状の製品を製作する技術です。食品工場の容器、半導体装置のフレームユニット、建築物の外装パネルなど、様々な分野でその技術が活用されています。中でも、抜き加工は、金属板にパンチとダイを用いて穴や形状を打ち抜く工程です。抜き加工は、タレットパンチプレスやプレス・レーザ複合加工機などの専用機を用いて行われます。これらの加工機は、金型を装着することで、丸穴、四角穴、長穴、異形穴、バーリング、ルーバーなど、多様な形状を高速かつ高精度に抜き出すことができます。特に、タレットパンチプレスは、多数の金型をタレットに装着し、自動で金型を交換しながら連続加工を行うことが可能なため、多品種少量生産から大量生産まで、幅広いニーズに対応できます。
金型を使用した抜き加工のメリット
金型による抜き加工は、レーザ加工に比べて加工速度が速く、加工精度も高いという利点があります。レーザ加工は、レーザビームを照射して材料を溶融・切断するため、熱影響による歪みや変形が生じやすいのに対し、抜き加工は、パンチとダイで材料をせん断するため、熱影響が少なく、高精度な加工が可能です。また、抜き加工は、一度に複数の穴や形状を加工できるため、加工効率に優れています
金型の選定と交換のコスト
抜き加工の精度は、金型の精度に大きく依存します。パンチとダイのクリアランス(隙間)は、加工する材料の板厚や材質によって最適な値が異なります。クリアランスが適切でないと、バリの発生や寸法精度不良などの不具合が生じる可能性があります。そのため、材料の板厚や材質に適した金型を選定することが、高精度な抜き加工を実現する上で不可欠です。
金型の交換には、時間とコストがかかります。そのため、設計段階で材料の板厚や材質を統一することで、金型の交換回数を減らし、コスト削減を図ることが重要です。また、汎用性の高い金型を選定することで、様々な形状に対応できるため、金型交換の頻度を抑制し、生産効率を向上させることができます。
特殊金型の存在とその利点
標準的な金型では対応できない複雑な形状や特殊な加工には、専用に設計・製作された特殊金型が用いられます。特殊金型は、顧客の要求に応じた独自の形状や機能を有しており、製品の高付加価値化に貢献します。ただし、特殊金型の製作には、高度な設計技術と精密な加工技術が必要となるため、コストが高くなる傾向があります。